摘要:五轴机床对机床装备制造业意义非凡,RTCP功能是衡量五轴机床性能的重要指标。 在RTCP执行过程中,需要通过添加旋转轴对直线轴进行非线性校正,因此旋转轴和直线轴的伺服动态特性需要进行测量和调整以保证加工动态精度。 本文简要介绍了RTCP的原理,设计了五轴动态精度测量算法,通过该算法对五轴机床的五个伺服轴特性按强弱顺序排序,从而优化和调整伺服参数。 以五轴叶轮的加工为例,比较了伺服参数调整前后加工的叶轮的加工质量,证明了该方法取得了较好的效果。
1.5轴数控机床比传统的3轴数控机床有很多优点。 例如,通过加工复杂的曲面或减少加工工序来提高加工效率。 但是,由于旋转轴的存在,在执行RTCP的过程中,旋转轴和直线轴是非线性运动的,因此需要控制五轴机床的动态特性,其动态精度成为了影响加工精度的主要因素之一。 五轴数控机床的动态精度主要来源于伺服系统的加减速响应性能、零件受力的变形、刀具的振动、主轴的转速、机床的进给大小等。 普通的伺服匹配测量方法不能准确地匹配直线轴和旋转轴。 五轴动态精度测量方法以RTCP功能特性为基础,建立直线轴和旋转轴的联动模型,以测量后的结果为依据,调整五轴数控机床的伺服参数,使伺服系统处于更好的状态,提高五轴联动数控机床的动态精度,提高机床的加工精度。
1. RTCP的原理介绍
RCP是旋转和工具中心点的缩写,是图1的刀具中心点编程。 启用RTCP后,刀具中心始终位于编程的XYZ位置,刀具中心始终位于编程坐标系中,旋转坐标的各运动通过编程坐标系XYZ的直线位移进行补偿。 使用RTCP,无需考虑五轴机床的结构参数,即可直接对以刀具为中心的轨迹进行编程,大大简化了五轴工艺编程,提高了加工精度。
2.RTCP的动态精度测量原理
在三坐标机床中,经常使用圆度测试来检测任意直线轴间的动态特性是否一致,但在五坐标机床的运动过程中,由于旋转轴的加入,必须对每个插补点非线性地补偿旋转轴的运动引起的直线轴偏差,因此旋转轴和直线轴间的动态特性由于旋转轴和直线轴的控制单位不同,所以不能像直线轴那样直接采用圆度测试。 采用本方法可以测试和排序五个轴的动态特性,为伺服参数的调整提供依据。
以x、y、z直线轴加上a、c转盘轴的5轴机床为例,分析5轴之间动态精度的调整方案。 在本测量方案之前,需要保证x、y、z直线轴按照常规三轴机床的调整策略进行直线轴间的匹配。
在RTCP运动中,a轴运动引起y、z轴运动,c轴运动引起x、y轴运动。 加工中,5个轴进行RTCP联动,但其动态精度测量过程也需要5个轴进行插补运动。 但是,建立5坐标RTCP动态测量模型很困难,即使能够建立模型,也无法通过反映动态匹配的指标直观地导出伺服参数的调整,因此需要分别测量2个旋转轴和相关的直线轴,简化RTCP动态测量模型在本例中,a轴和y、z轴是一组测量,c轴和x、y轴是另一组测量。 由于y轴同时与a轴和c轴相关,因此在调试过程中,y轴伺服参数在一个测量完成后,在另一个测量过程中不会进行调整。
以旋转轴a为例,RTCP有效时,a轴旋转时,与其相关的y、z轴的实际运动轨迹是以旋转半径为中心的圆弧。 这里需要测量的内容是y、z直线轴之间的匹配和a、y、z旋转轴与直线轴之间的匹配。 具体的测量过程如下
(1) y、z直线轴之间的匹配
在有旋转路径的象限中选择几个机床的实际坐标采样点,计算各采样点的实际位置与指令位置之间的误差值(图2 ),基于各象限误差的总和
和采样点的数量通过以下公式求出不匹配值。
计算结果:大于零,y轴强于z轴时小于零,y轴弱于z轴。 对c轴、x轴、y轴的处理方法与a轴、y轴、z轴相同,上述测量过程是常用的圆度测量方法。
) a、y、z旋转轴与直线轴的匹配
在有旋转路径的象限中选择几个机床的实际坐标采样点,可以根据y、z轴的实际位置计算出a轴的最佳位置图3的值。 a的实际位置通过采样得到,计算a轴的最佳位置和实际位置的误差值,根据误差的总和和采样点的数量由计算式: /得到误差的平均值,可以判断直线轴和旋转轴的强弱。 c轴和x、y轴的判断方法与a轴的方法相同。
c">根据上面测定方法,确定五个轴的强弱程度的排序,以此来进行伺服参数的调整。调整过程中,旋转轴的伺服参数不进行调整,只调整直线轴的伺服参数。
五轴动态精度测定流程见图4所示。
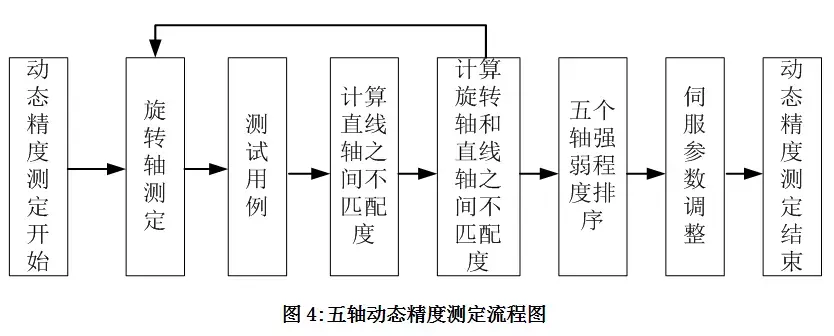
1. 功能测定及结果分析
为了测试算法的可行性,对叶轮加工做了对比实验,实验过程及结果如下:
3.1实验装置
1、DMG的AC双转台五轴机床(图5);
2、FANUC;
3、SSTT采样软件。
简单介绍一下SSTT采样软件,SSTT是伺服调整工具(Servo Self Test Tools)的简称,主要用于配置FANUC数控系统的机床在线调试、诊断过程,也可以作为一种离线数据分析工具。本实验主要通过SSTT工具采集各轴运动机床实际坐标数据,应用本文提出五轴动态精度测定方法来进行伺服参数调整,从而提高五轴RTCP动态特性。
3.2实验方案
第一步,按照机床原定的伺服参数,加工叶轮的流道、大叶片及小叶片。
第二步,采用RTCP动态精度测试方法,计算直线轴与直线轴、旋转轴与直线轴之间的不匹配度情况:
(1) 以A轴测试为例,在SSTT采样软件上设置好测试程序的相关参数,生成采样程序并发送到下位机,测试程序如下:
%12345; A轴行程-90度到0度,开启RTCP功能,实现A、Y、Z轴联动;
G54 X-10 Y-20 Z-30 F2000
G01 A0
G128
M00
G01 A-90
M00
G01 A0
M30
机床运行该程序,由SSTT采集各轴的机床实际位置。当程序运行到G43.4 H1时,RTCP功能开启,运行到第一个M00时,SSTT采样开始,运行到第二个M00时,SSTT采样结束。采样过程中,以时域图和圆轨迹图显示采样情况,如图6和图7。

(2) 由采集的各轴的机床实际位置,用本文上述的RTCP动态精度测试方法,计算直线轴与直线轴、旋转轴与直线轴之间的不匹配度。
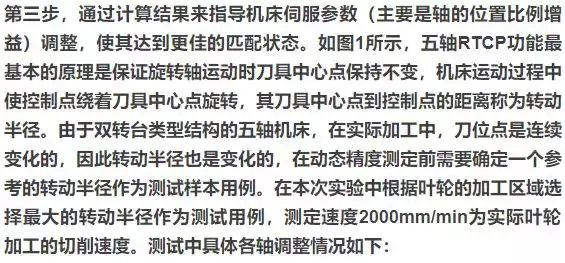
(1)A轴
Y、Z、A轴伺服匹配见表1。
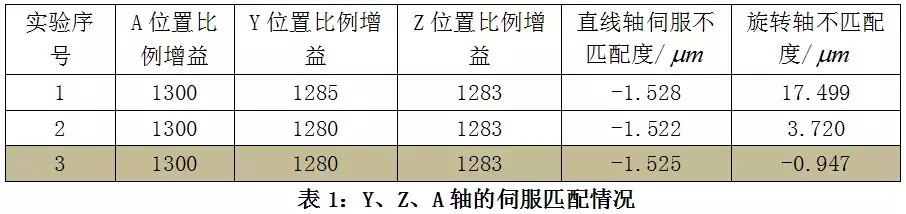
(1)C轴
X、Y、C轴的伺服匹配见表2。
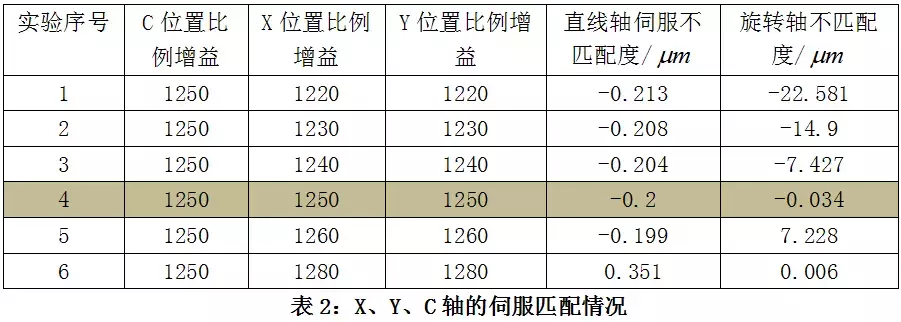
3.1实验结果与分析
(1)调整前流道靠近小叶片顶端区域有明显的过切痕迹,调整后过切痕迹
消失,表面光滑, 见图8。
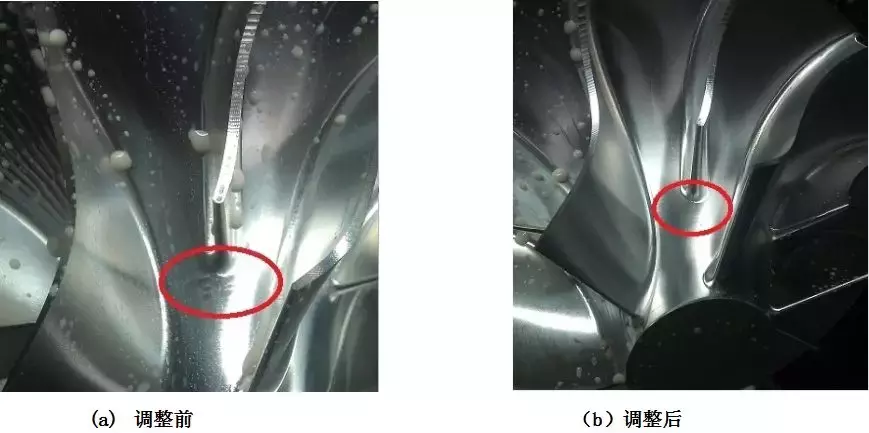
(1)调整前大叶片背面底部有明显的过切痕迹,调整后过切痕迹消失,表面光滑,见图9。
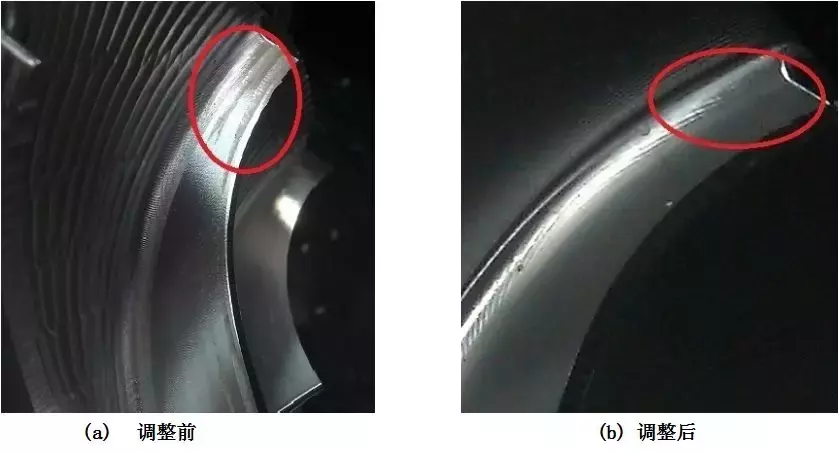
1. 结语
